Commercial Roofing Systems
Introducing Legacy Roofing Contractors, our dedicated commercial roofing division with over 65 years of experience, specializing in servicing and replacing roofs for Commercial and Industrial clients.
Our History
Herman Krumwiede founded Krumwiede Roofing in 1952. His Grandson Mark Washburn now owns Legacy Roofing Contractors, with a rich family history in the roofing industry. Mark opened Shingle Company Construction and Legacy Roofing Contractors in La Grange Park, IL in 2005.
Commercial Roof Repair vs. Replacement
Choosing between repair and replacement for your commercial roof is crucial. As leading experts in commercial roofing, Legacy Roofing Contractors offer guidance based on extensive experience. Reach out for an affordable evaluation, considering factors like roof type, condition, age, and climate for tailored recommendations.
Commercial Roof Maintenance Tips
Proper maintenance is crucial to prolonging your commercial roof’s lifespan. Legacy Roofing Contractors, a trusted and licensed roofing contractor, conducts thorough inspections and prioritizes adherence to manufacturer’s specifications and local regulations. Schedule inspections at least once every two years and after significant weather events.
Commercial Roof Warranties Guide
Understanding commercial roofing warranties is crucial. Legacy Roofing Contractors offers warranties starting at 10 years for new roof systems, covering material defects and workmanship issues related to installation. Trust us for reliable commercial roofing warranties and peace of mind.
Choosing the Best Commercial Roofing Material
Selecting the ideal commercial roofing material is essential. Legacy Roofing Contractors assists in finding the perfect roofing system tailored to your needs. Trust us to guide you towards the optimal commercial roofing material for your unique requirements.
Exploring the Features of Liquid and Spray Foam Roofing Systems
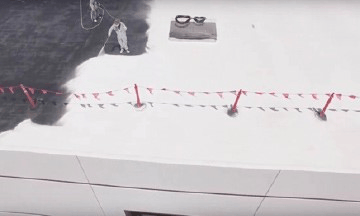
Silicone Roof
Liquid and spray foam roofing systems offer a range of features and benefits worth considering. Liquid applied roofing options encompass various materials such as hot and cold polymer-modified asphalt, single-component asphalt, coal tar-extended urethane, and two-component urethane elastomers.
To ensure proper performance, these systems require thorough preparation of the substrate, which should be dry, dust-free, and have patched cracks. One of the key advantages of liquid applied coatings is their high elasticity and self-flashing properties, making them suitable for application on contoured surfaces. However, it’s important to note that the durability of spray foam in cold and wet climates has faced challenges in the past. Incorrect installation can undermine its effectiveness, making it an unfavorable choice.
When considering liquid and spray foam roofing systems, it is essential to consult with experienced professionals who understand the intricacies of these materials. Trust Legacy Roofing Contractors for expert guidance and ensure the best choice for your roofing needs.
Exploring the Features of Steel and Metal Roof Systems
Steel and metal roof systems offer unique advantages and are commonly used in commercial applications, particularly for steep slope roofs with pitches greater than 4in12. Metal roofing has a rich history, dating back to ancient times, with materials like bronze and lead being utilized in renowned structures such as Rome’s Pantheon and medieval European cathedrals and castles.
Modern low slope metal roofs often feature corrugated galvanized steel coated with zinc. However, commercial metal roof systems also utilize materials like copper, aluminum, stainless steel, and tin. The benefits of metal roofing are manifold, including its exceptional longevity and resistance to heat. Metal roofs are highly durable, capable of withstanding high winds and offering significant impact resistance.
It’s important to note that metal roof systems come with a higher cost compared to other low slope roofing materials. Structural metal roofing, commonly known as “standing seam” roofing, consists of interlocking panels that run vertically along the roof. These panels can be pre-painted, have a mill finish, or a clear acrylic finish. Machine seaming is typically required during the installation process for most metal roofing systems.
When considering steel and metal roof systems, consult with experienced professionals like Legacy Roofing Contractors. We have the expertise to guide you in selecting and installing the ideal metal roof for your commercial needs, ensuring longevity, durability, and aesthetic appeal.
Exploring the Benefits and Durability of Built-Up Roofing (BUR) Systems
“Yelling Hot tar! in the morning,once it was boiling hot and ready to be pumped up to the rooftop was always my favorite way to start a day of Built up roofing”!
– Mark Washburn, President – Legacy Roofing Contractors
Built-Up Roofing (BUR) Systems have been a popular choice in North America for over a century, offering exceptional durability and longevity. These systems consist of alternating layers of bitumen (asphalt) and roofing fabrics known as roofing “felt.” The felt membrane is reinforced with either glass-fiber mats or organic mats, creating a robust and long-lasting roofing surface. The number of “plies” indicates the number of layers of felt, with a higher ply count denoting a thicker and more robust flat roof membrane system with layers of tar in between.
One of the key advantages of BUR systems is their redundancy. If one layer deteriorates, the remaining layers provide immediate protection, ensuring the integrity of the roofing system. These systems exhibit excellent tolerance for building stress, resistance to thermal shock, high puncture resistance, and impressive membrane strength and toughness, guaranteeing long-term durability.
BUR systems offer flexibility in their composition, including options such as SBS, fiberglass, or organic felts, catering to a wide range of building requirements. The repetitive layering is a defining feature of this system, contributing to its superior fire resistance. Additionally, BUR systems can incorporate reflective surfacing options, providing maximum membrane protection, exceptional puncture resistance, and high resistance to foot traffic and mechanical maintenance.
Legacy Roofing Contractors, under the guidance of President Mark Washburn, specializes in Built-Up Roofing (BUR) Systems. With our expertise and commitment to quality, we ensure the installation of durable and reliable roofing solutions. Trust Legacy Roofing Contractors for all your BUR system needs, delivering exceptional performance and peace of mind.
Exploring the Benefits and Installation of Modified Bitumen Roofing Systems
Modified Bitumen roofs, also known as “Modified” roofs, are constructed using factory-fabricated layers of asphalt that have been modified with rubber or plastic additives. This modification enhances the flexibility and longevity of the asphalt, making it an excellent choice for roofing applications. Bitumen, a sticky, black liquid or semi-solid form of petroleum, serves as the base material for these roofs, which are commonly used in both roads and roofing.
There are two primary types of modified bitumen membranes in use today: APP (atactic polypropylene) and SBS (styrene butadiene styrene). APP and SBS refer to the polymers added to the asphalt, providing specific properties to the membrane. Reinforcements such as fiberglass, polyester mats, and scrims, which are fabrics made from continuous filament yarn, are utilized to enhance strength and stability.
Modified bitumen membranes are typically installed in two- or three-ply systems. SBS membranes are either mopped down using hot asphalt or heat welded, allowing the asphalt to melt and flow onto the substrate. Seams are sealed using the same technique. The membrane system can be held in place on the roof by fully adhering the base sheet, mechanically attaching it, or using ballast. APP Bitumen, on the other hand, is heat welded or “torched” down in a similar fashion over the base sheet.
One of the key advantages of modified bitumen roofing systems is their ease and speed of installation. They are relatively quick to install, easy to maintain, and cost-efficient. Modified membranes can be applied through hot mopping, similar to traditional Built-Up Roofing (BUR), or as a torch-down product.
When it comes to modified bitumen roofing systems, rely on the expertise of Legacy Roofing Contractors for professional installation, maintenance, and cost-effective solutions. Our team is experienced in working with modified bitumen roofs, ensuring quality and durability for your roofing needs.
Advantages of Single Ply Membrane Roof Systems
Over the past four decades, the single ply membrane market has experienced remarkable growth. Single ply roofing systems have established themselves as reliable commercial roofing solutions, offering an extended service life and requiring minimal maintenance.
The emergence of the single ply membrane market can be attributed to multiple factors, including the escalating prices of petroleum during the energy crisis of the 1970s. Additionally, dissatisfaction with conventional bituminous roofing systems created a demand for alternatives. Single ply membranes presented a favorable solution due to their lighter weight, which made field installation less labor-intensive compared to conventional systems. The Single Ply Roofing Industry (SPRI) classifies single ply commercial roofing membranes as “flexible sheets of compounded synthetic materials that are manufactured in a factory with stringent quality control requirements.”
Single ply roofing systems provide exceptional strength, flexibility, and long-lasting durability. The pre-fabricated sheets offer consistency in quality, while the versatility of attachment methods and wider applicability provide numerous advantages over traditional bitumen or asphalt roofs.
There are two major categories of single ply membranes:
Exploring Thermoset and Thermoplastic Single Ply Membrane Roof Systems
Single ply membrane roof systems can be categorized into two main types: thermosets and thermoplastics, each offering unique properties and advantages.
Thermoset membranes are manufactured from rubber polymers, with the most commonly used polymer being EPDM (Ethylene Propylene Diene Monomer). EPDM is a durable rubber roofing solution available in black and white variants. Thermoset membranes excel as roofing materials due to their ability to withstand the damaging effects of light and common chemicals found on roofs. However, EPDM membranes may be more susceptible to puncture damage due to their thin and soft profile. For detailed information on EPDM roofing resources, the EPDM Roofing Association (ERA) provides valuable insights.
On the other hand, thermoplastic membranes are composed of polymers that soften when heated and harden when cooled. These pre-fabricated sheets are applied on-site using standard installation techniques such as fully adhered, mechanically attached, or ballasted methods. The installation process involves heat or solvents to weld the membranes together, creating a bond strength that matches or exceeds the strength of the base material. The most common types of thermoplastic roofing membranes are polyvinyl chloride (PVC) and blends or alloys of PVC and thermoplastic polyolefins (TPO).
Both thermoset and thermoplastic single ply membrane systems offer advantages for commercial roofing applications. Understanding the characteristics and differences between these membrane types is crucial for making informed decisions regarding your roofing needs. Legacy Roofing Contractors can provide expert guidance and installation services for thermoset and thermoplastic single ply membrane roof systems, ensuring a durable and efficient roofing solution for your commercial property.
Importance of Insulation and Vapor Retarders in Roof Systems
Insulation plays a critical role in roof systems, offering multiple benefits beyond energy conservation. Its primary function is to minimize heat transfer into or out of a building, and it is typically installed just below the roofing membrane or waterproofing system. Various types of insulation are available, including rigid or semi-rigid boards and panels made from materials such as polystyrene, polyisocyanurate, fiberboard, fiberglass, and composite insulating materials.
Polyisocyanurate (iso) is a closed-cell, rigid foam board widely used in roof and wall assemblies of both commercial and residential buildings. Renowned for its exceptional thermal performance, it is a preferred choice among architects, builders, building owners, and contractors. In fact, it is the most commonly utilized and readily available insulation product in North America. ISO insulation offers stability and compatibility with a variety of roofing systems, making it highly versatile and effective.
In addition to insulation, the inclusion of vapor retarders in roof systems is essential. Vapor retarders help control moisture movement through the roofing assembly, preventing potential damage caused by condensation. Properly installed vapor retarders contribute to the long-term durability and performance of the roof system.
When it comes to insulation and vapor retarders, Legacy Roofing Contractors understands the importance of selecting and installing the right materials for optimal energy efficiency and protection. Our team of experts is equipped with the knowledge and experience to guide you in choosing the most suitable insulation and vapor retarder solutions for your specific roofing needs.